How Data Analytics Can Increase Manufacturing Efficiency
Within manufacturing, there is a desire to make efficiency and productivity improvements throughout every part of the production process. Realizing that increases in profitability can often only be achieved by optimising complex industrial processes at the source, many organisations are turning to programmable automation controls and optimisation software to accomplish this. While these tools are rapidly evolving to keep up with changing industry demands, complexities such as communications latency and network security can be a challenge.
While Programmable Logic Controllers (PLCs), developed in the 1970s, offer much greater flexibility for programming compared to relay-based systems, they are still programmed using ladder-logic to mimic the appearance of wiring diagrams. Programmable Automation Controllers (PACs) provided progression by offering a single platform that operates in multiple domains such as motion, discrete and process control applications, offering an even higher level of flexibility and interoperability with enterprise systems. However, they are unable to dynamically adjust to changing business objectives and are viewed as static components, heavily constrained by the design specification at installation. While most manufacturers still use PLCs and PACs, the industrial Internet era has created the opportunity for analytics tools to evolve. Data analytics tools are becoming more complex to address the increasing need for flexibility, and presenting more opportunities to achieve operational efficiency, cut costs and drive productivity.
Device and equipment integration
The IIoT involves many physical devices that produce a large amount of data. Integrating and organising this data is critical to gaining meaningful and actionable insights. Data and analytics can help tie equipment operation to business objectives and performance. When devices and equipment are successfully integrated within the plant as well as with business automation tools, it becomes easier to develop condition-based maintenance strategies and improve Overall Equipment Effectiveness (OEE). Condition-based maintenance is a strategy based on monitoring the actual condition of equipment and deciding what maintenance is required based on early warning signs of failures, as opposed to a calendar-based maintenance. This works on many types of equipment, especially if it performs a consistent task such as a pump, motor, compressor or fan. Technicians look at long-term trends of key process parameters for the equipment and learn to spot changes in behaviour indicating mechanical problems are forming, and advanced users may develop statistical models of the equipment and compare existing behaviour to the model in order to locate potential problems.
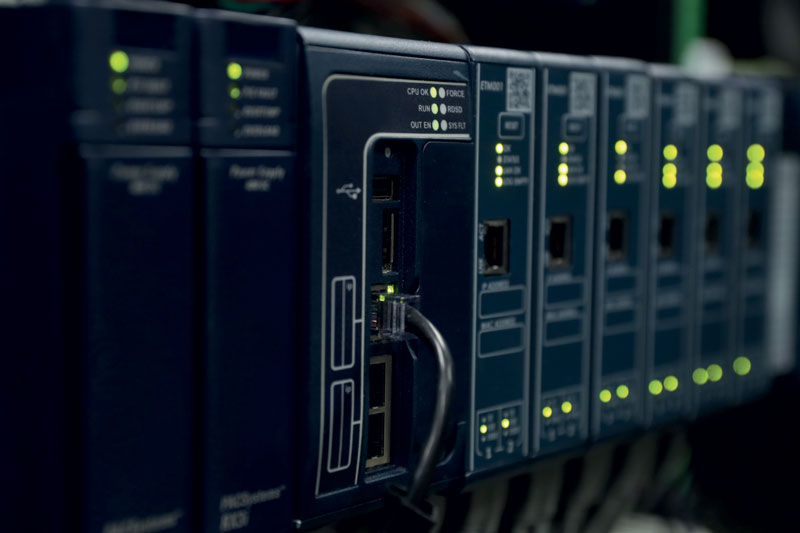
High-performance Edge computing
The latest advances in processor technology is rapidly increasing the performance of industrial devices, leading to an expanded and often multi-purpose role for edge controllers. One way to get the most of out of the inherent multi-core processing power of the new generation of outcome-optimising edge devices is by virtualising programmable automation control systems. The ability of hardware virtualisation techniques to run multiple operating systems in tandem provides a new approach to the optimisation of control processes. with analytics and optimisation applications run at the machine level without directly impacting or hindering deterministic, real-time control.
Real-time data
By capturing and analysing data and using that data in real time to adapt to a wide range of variables, the latest generation of programmable automation control systems provide enhanced productivity, efficiency and security to any operation.
Because every operation is different and every organisation will have different types and numbers of connected devices and processes, the more flexibility and connectivity an optimisation software offers when leveraging external data for analysing and optimising industrial operations, the better.
Edge technology also plays an important in role in real-time data processing. While the cloud can do wonders in allowing a centralised way to process and store massive amounts of data, there continues to be a problem with latency for some applications where even a split-second delay in sending and processing data can hinder an operation. For those applications, processing data at the edge instead of sending it to the cloud removes this delay and decisions can be made immediately, resulting in true real-time response.
Local web-based HMIs
Human-machine interfaces (HMI) can access data at the device using a web browser. The web-based HMI offers many benefits, one of the most significant being that it is accessible from anywhere. Web-based HMIs also can be accessed on any mobile device, which can reduce a facility’s device footprint and support the new generation of workers who prefer to use these tools while working physically in or away from the plant. A web-based application can be developed once and then provided to any device supporting typical web browsers, which can cut costs and save time during development and troubleshooting.
Remote monitoring
It can be challenging for OEMs to assess the health of their machines and systems, especially when they have large fleets or numerous remote assets to track. Without connectivity, the OEM service teams need to travel to each customer using their equipment either proactively or reactionary because something has already failed. The first scenario can potentially involve a lot of travel time to visit equipment that is running just fine. The second isn’t much better, because the OEM is visiting a customer who is already impacted by equipment failures, which might create reputational harm and the potential loss of future sales. Therefore, the benefit of real-time information, especially when the information is by exception, is that the OEM service teams have insight into the health of their assets remotely. This way, OEMs can be proactive, servicing equipment during early warning signs of failure, rather than when the equipment has actually failed. When OEMs can remotely and securely collect and analyse data, they easily can provide actionable information for maintenance engineers and end users who have purchased the equipment. With access to detailed fault logs, hardware and firmware versions, and sweep time, operators can debug faults remotely, greatly reducing operational costs and unplanned downtime. Remote monitoring and diagnoses using cloud-based services also provides OEMs with insight into how customers are using their machines, and can optimise asset performance, processes, and profitability.
About the Author: Steve Ward is director of application engineering EMEA, Emerson.