Efficiency and Energy Saving in the Printing Industry
Printing and vacuum industry: how to make circuits more efficient and save money? Vuototecnica supports its customers with its Graphic Division line. In particular, its compact, light and efficient PA/PS multi-stage pneumatic vacuum generators are able to ensure substantial energy savings.
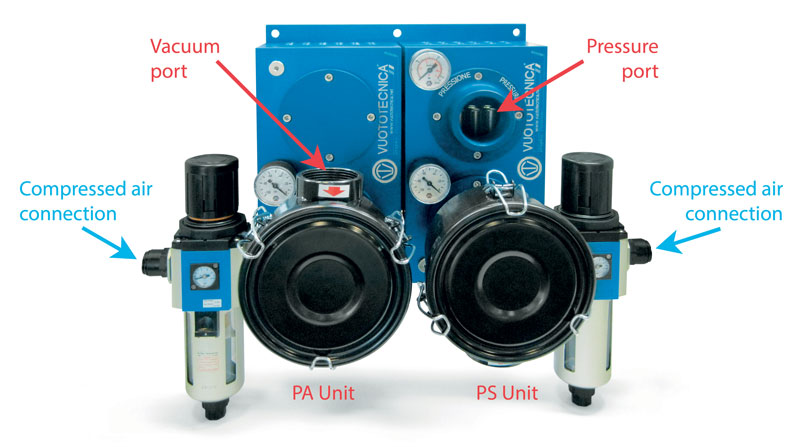
In the printing industry, vacuum is used in several applications. One of these is sheet feeding in offset printing presses, from input to output, after printing. Low pressure air can be used to separate the sheets. The speeds at which these steps take place are very high indeed and make these operations a tightrope walk between vacuum and blown air for which you need to be prepared. A balance that must be studied and managed.
In most cases, despite the fact that the feeders have only 6-8 small diameter suction cups, air and vacuum are generated and excluded by a pump that is too large, and positioned too far away from the machine, supplied with a really bulky series of piping. The end customer is never to blame, in fact he relies on “advisors” that are used to build centralized vacuum systems, with large pumps placed in a single point. In doing so, they make sure they can relegate the mess of the encumbrance to a corner and compensate the distance of the machinery with the length of the pipes and with a high flow rate.
However, the exaggerated flow rate is choked by the small pipes that usually feed the suction cups. And the same problem of oversizing and bottleneck is found in relation to the low-pressure distribution (max +0.6bar) which, generated by the electric pump, reaches the small nozzles that blow air, and used for the separation of the sheets.
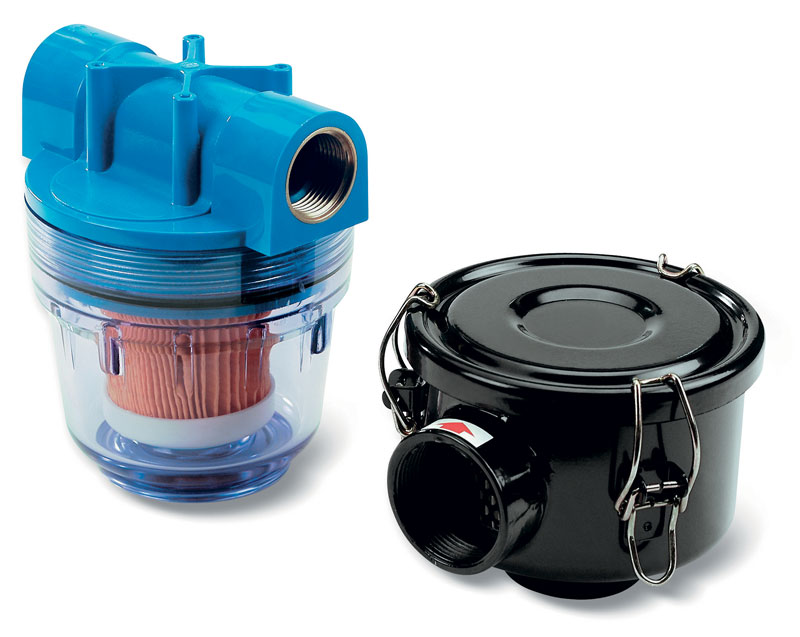
The enormous energy expenditure can be avoided
With these systems the energy expenditure becomes enormous: the customer is forced to keep the pump motor always on at maximum power while the two channels (vacuum and air) are partialized. By means of manual valves, for the vacuum channel, atmospheric is fed into the pipe (loss) while for the low-pressure channel it is released into the atmosphere (another loss). The problems generated by the use of such oversized pumps is evident. These losses especially on the vacuum channel, also increase the wear of the blades on the internal stator of the pump due to friction; besides space and inefficiency, wear is another major issue. Finally, in the summer period, overheating of the pumps is another problem as it may lead to downtimes and extra maintenance costs for the companies operating in the paper and printing industry. End customers invest a lot of money without any benefit in terms of efficiency. To make things worse, oversized pumps require skilled technicians for their maintenance, and costs consequently rise…
No more waste of energy, time and money with the new solution
In such applications Vuototecnica can support customers, helping them avoid energy wastes, time and money… The company has designed a line of PA/PS multi-stage pneumatic vacuum generators, less bulky, lighter and more efficient. PA/PS pneumatic vacuum generators allow the vacuum (or pressure) degree and the flow rate to be adjusted according to the air pressure. Customers can manage the pumps with proportional valves for compressed air and limit the consumption to a minimum, depending on the weight and porosity of the paper and the cardboard processed by the printing machine. Moreover, these pumps are quiet (60-65dB) and do not overheat. The air used to separate the sheets of paper is fresh and free of impurities, condensation or oil vapors. The electrostatic charges generated by the blown hot air of traditional electric pumps is also reduced.
Construction materials are of the latest generation, which makes it possible to reduce the weight and overall dimensions and to allow them to be fitted on board, not further away, thus also reducing the piping. Maintenance is required to clean the suction or blower filters only.